補聴器専門店「あそう補聴器」マーケティング担当の石橋です。
この度、補聴器メーカーの日本本社と工場を見学させていただきましたのでレポートさせていただきます。
今回伺ったのは、
補聴器とヘッドセット産業の両方から深い洞察と知識を得ながら、
耳/聴覚学、音声、ワイヤレス、および小型化の分野で世界をリードするオーディオソリューション企業「GNグループ」の
日本法人「GNヒアリングジャパン株式会社」です。
各部門の様子と補聴器がどのように作られるのかを、写真と共にお伝えさせていただきます!
GNグループ全体について
GNグループには2つのブランドがあります。
![]() |
リサウンド 補聴器事業 |
![]() |
ジャブラ オフィス専用ヘッドセット /消費者向けヘッドホン事業 |
GNグループ本社はコペンハーゲン
デンマークの首都「コペンハーゲン」にGNグループの本社があり7500人もの従業員がデザインや研究・開発を行っています。
150年の歴史と100カ国での販売
GNの歴史は150年以上もあり、補聴器&ヘッドセットを100カ国以上で販売しています。
補聴器だけでなくヘッドセットも研究開発しているのが特色の一つです。
当店でも、 「リサウンド・ネクシア」や、「リサウンド・オムニア」をはじめとした様々な補聴器を当店のお客様にもご愛用いただいております。
技術革新の歴史
GNは他社があまり取り組まない分野に挑戦するユニークな補聴器ブランドです。
それゆえ、業界初となる技術が多く、後から他社に取り入れられ、補聴器業界のスタンダートとなることがあります。
1989年 | ワイド・ダイナミック・レンジ・コンプレッション 小さな音と大きな音の適正なバランスで自然なきこえを再現 |
1992年 | デジタルハウリング処理技術(DFS) 不快なピーピー音を瞬時に抑制 |
2003年 | オープンフィッティング 耳の穴をふさがないので、自分の声がこもりづらい |
2010年 | 2.4GHzワイヤレス技術 離れた声やテレビの音を補聴器に直接送信し、補聴器の活用範囲が拡大 |
2014年 | スマート補聴器 iPhone,iPadの音声や設定がダイレクトに補聴器と通信可能 |
2017年 | リサウンド・アシスト遠隔サポート どこにいても安心の遠隔サポート |
2020年 | 耳の穴に配置した3つ目のマイク「マリー」 耳本来の集音を活かした自然なきこえ |
2023年 | Bluetooth LE Audio搭載 ストリーミング音質の向上とAuracast™対応 |
GNヒアリングジャパン本社は横浜みなとみらい
未来的なウォーターフロントの地区、みなとみらいにGNヒアリングジャパンの本社はあります。
横浜美術館やランドマークタワー、国際会議場と展示ホールを持つパシフィコ横浜、クィーンズスクエアなど、
文化施設や商業施設が立ち並ぶ みなとみらい21中央地区の中心にある「みなとみらい駅」。
その「4a」出口を出ると・・・
屋根が繋がっているビルが・・・!
それがGNヒアリングジャパンが入居している「MMパークビル」。
みなとみらい駅から雨に濡れず、夏の日差しも避けて行くことができます。
エントランスは重厚な雰囲気で、アートが投影されていました。
ジムやクリニック・コンビニ・会議室などが入居しており、とても便利!
エレベーターで8階まで上がり・・・
入り口を入ると・・・
エントランスにはGNグループ本社のあるデンマークらしいオブジェと最新補聴器「リサウンド・ネクシア」のタペストリーが飾られていました。
駅や空港、公共施設などで今後様々なアナウンス放送などの音を、無線で聴くことができるようになっていく予定。
こうした最新のテクノロジーを積極的に取り入れるのがGNグループの特色の一つです。
ミーティング
補聴器専門店として現在15店舗を運営している当社が実際にGNの補聴器を取り扱っていて感じる良さや
今後さらに補聴器ユーザーにご満足いただくための課題などについてミーティングをさせていただきました。
代表取締役 社長 マーティン アームストロング
マーティン アームストロングは
1967年3月生まれ、イングランド東北部のモーペス出身。
1988年にイングランド南部のレディング大学を卒業後、
石油探査地質学者として石油掘削プラットフォームで働いていたそうです。
その後、製薬会社に勤務。
2007年に日本に移住し、
製薬会社の「ノバルティスファーマ」(本社はスイス)、
動物用医薬品の「エランコジャパン」(本社は米国)、
女性疾患における診断機器、診断薬、治療用医療機器の「ホロジックジャパン」(本社は米国)を経て、
2022年3月からGNヒアリングジャパン代表取締役社長に就任されています。
補聴器ユーザーのニーズについて興味を持って話を聞いてくださいました。
ピーター ユステスン
ピーター ユステスンは、
GNヒアリングジャパンではなく
デンマークのGNグループ本社の補聴器部門でアメリカ以外の80カ国以上を担当している方。
年に1回程度日本を訪れているとのこと。
補聴器の充電器や補聴器の乾燥ケア等に関するお客様のお悩みをお伝えしたところ、
他国であまり聞かない内容だったとのことでしたが、とても真剣に興味を持って聞いてくださいました。
また、充電式耳あな型補聴器のサイズに関するお話をしたところ、
耳掛け型の小型化についてはかなり実現できたので、次は耳穴型の小型化をしていきたい。」
と話してくださいました。
『補聴器』である以上、これからも音質についてはリーダーであり続けたい」
と熱く語ってくださいました。
ピーター ユステスンは製品開発にも関わる方なので、今後の製品に活かしていただけたら嬉しいですね。
カスタマーサービス部門
カスタマーサービス部門の入り口付近の壁にはコペンハーゲンのニューハウンの街並みが貼られていました。
ユニークなオフィスですね。
カスタマーケア部門
この部屋は工場や部署とは異なるハートフルな雰囲気でした。
8名体制で対応されています。
カスタマーケア部門のマネージャー竹澤舞衣子氏
販売店から電話相談を受けるタイミングは
販売店の方が、まさにお客様との接客中である場合が多いため、
迅速かつ正確な回答ができるよう、セールスフォースのデータベースを活用しながら
テクニカルサポート部門や修理部門と迅速な情報共有を行って対応されているとのこと。
システムを活用し、着信の待機ができているスタッフの残り人数を常にモニターしていて、
例えば社内での電話ミーティングなどを行っている際に、
着信待機ができるスタッフが少なくなった場合には一旦電話を切るなどして、
必ず販売店からの電話相談にすぐに出ることができるようにしているとのこと。
活字のチャットでの相談もできるようにしたりなど、さまざまな方法で相談が受けられるように体制をアップデートさせているそうです。
テクニカルサービス部門
テクニカルサポートのマネージャー 木村秀則氏
「製品仕様」「器種選定」「接続方法」「調整相談」「ペアリング手順」「ソフトのインストール」「トラブルシューティング」といった
テクニカルに関する対応を電話対応で行われているとのこと。新しいソフトの検証も行なわれているそうです。
技術的なトラブルに対応していただける方がいらっしゃるので当社としても、とても頼もしく感じております。
テクニカルサービス部門は3名体制ですが、この日会社に出勤されていたのは木村氏のみ。
一般的なメタル回線ではなくインターネット経由の電話を採用し、リモート勤務も可能な体制が整っているそうです。
木村氏自身も先日ぎっくり腰になってしまったが、テレワークで滞りなくサービスが継続できたとのこと。
今の時代に合わせて働き方もアップデートされていました。
フリーアドレススペース(経理・マーケティング・営業等)
オフィスはフリーアドレス形式を採用。
ハイカウンターや昇降式デスク、外付けディスプレイのあるデスクなど、
その日の業務内容や気分に合わせてデスクを選ぶことができます。
連日続けて同じ席に座ってはいけないというルールもあるとのこと。
新鮮なコミュニケーションから新しいアイデアが生まれそうですね。
休憩ブース
工場のドアの中は神奈川県庁の公認で医療機器を製造するエリアとして登録されており、
工場の中では一切の飲食物の持ち込みが禁じられていますので、工場の外に飲食ブースが別途設けられています。
製造部門
工場内についてはITEプロダクションマネージャーの
近藤 心 氏に案内をしていただきました。
荷受→仕分け
まずは荷受けのお部屋。
仕入れ・修理・新規作成の為の耳型(インプレッション)など全ての荷物が届くので
ダンボールの開梱を行なった上、
「新規のオーダーメイド=黄色」
「耳あな型補聴器の修理=緑」
「耳かけ型補聴器の修理=ピンク」
などわかりやすく色分けして仕分けされます。
受付→システム登録
ここからは新規のオーダーメイド補聴器の製造工程をご紹介します。
まずは、耳型(インプレッション)を確認し、注文・仕様内容を基幹システムに登録していきます。
この基幹システムを通じて生産管理や在庫管理が行われます。
耳型(インプレッション)の補修
まずは耳型(インプレッション)(※写真の緑色の物)の、
不要な部分の切り落としや、欠損している部分の補修が行われます。
この耳型はオス型にあたる部分ですが、GNでは毎回この耳型を使って、メス型が作られます。
イメージとしては、粘土にギューっとこのオス型を押し込んだようなものです。
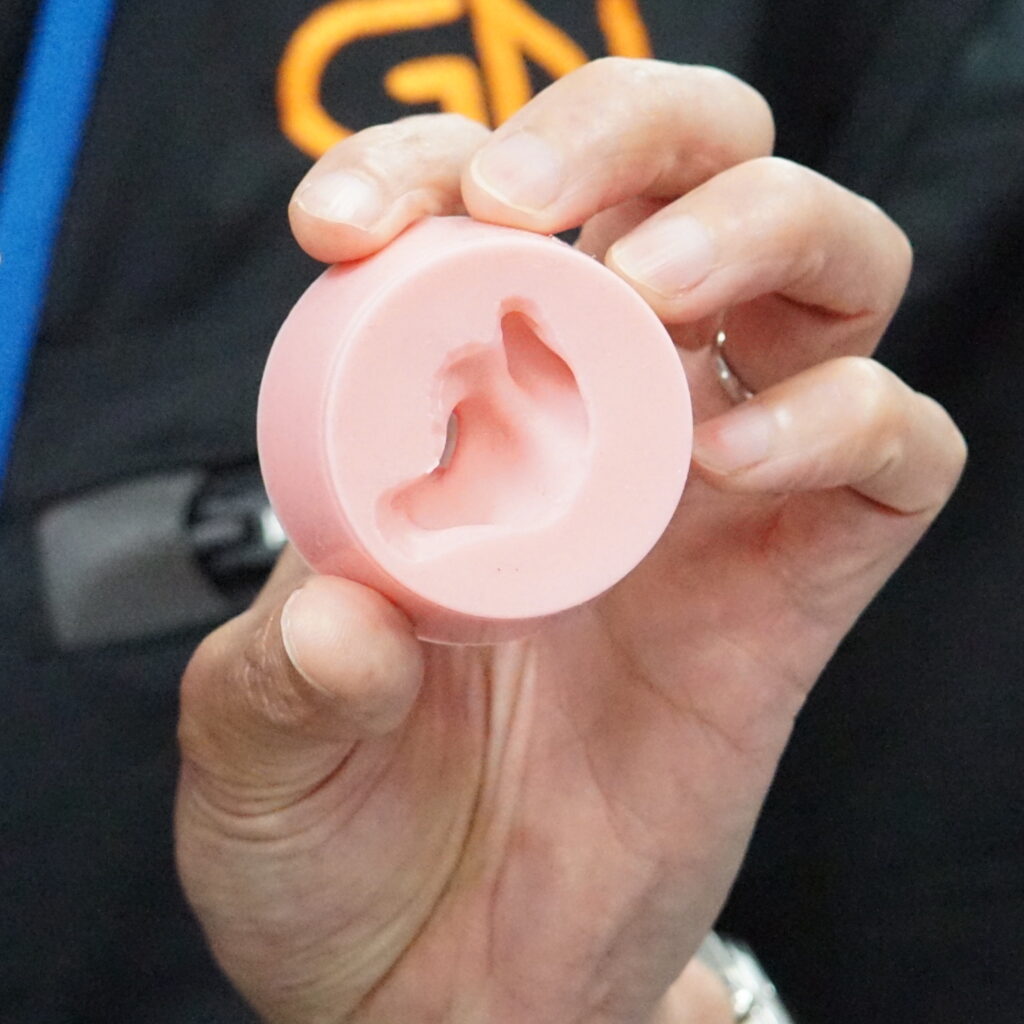
メス型
このメス型の形がちょうど、補聴器装用者の耳の形と一緒ということになります。
後の工程で、補聴器の形が出来上がってきた際に、このメス型に実際に装着して形のチェックが行われます。
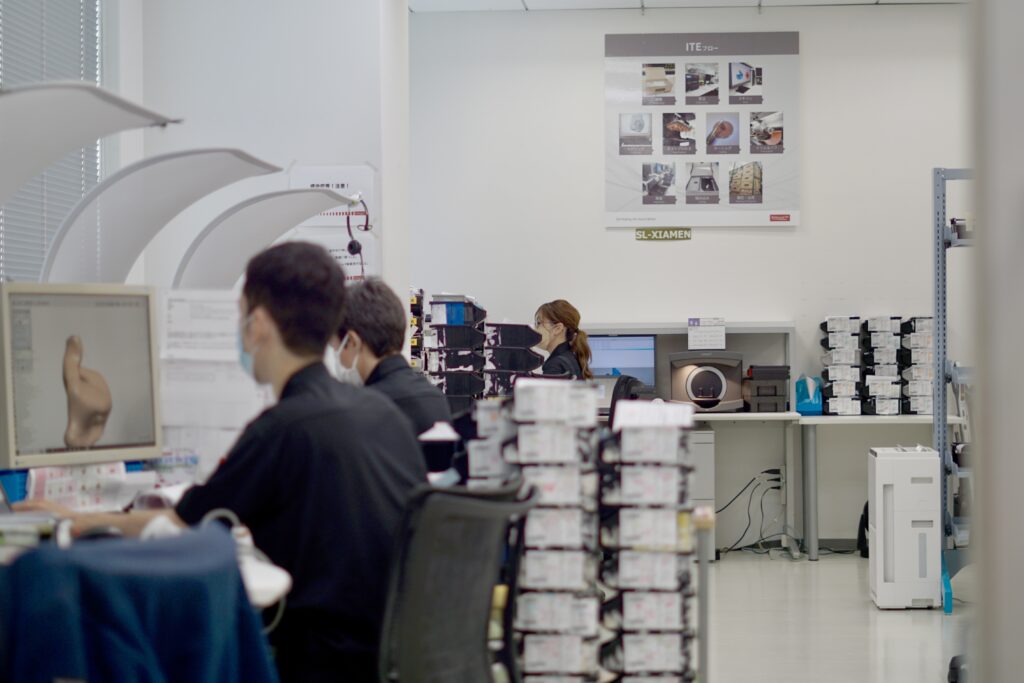
モデリング担当者等が作業をされてる様子。
耳型(インプレッション)の3Dスキャン
こちらが3Dスキャナですが、いきなりスキャンを行うのではなく
スキャンを行う前に3Dスキャナのバリデーションチェックが行われます。
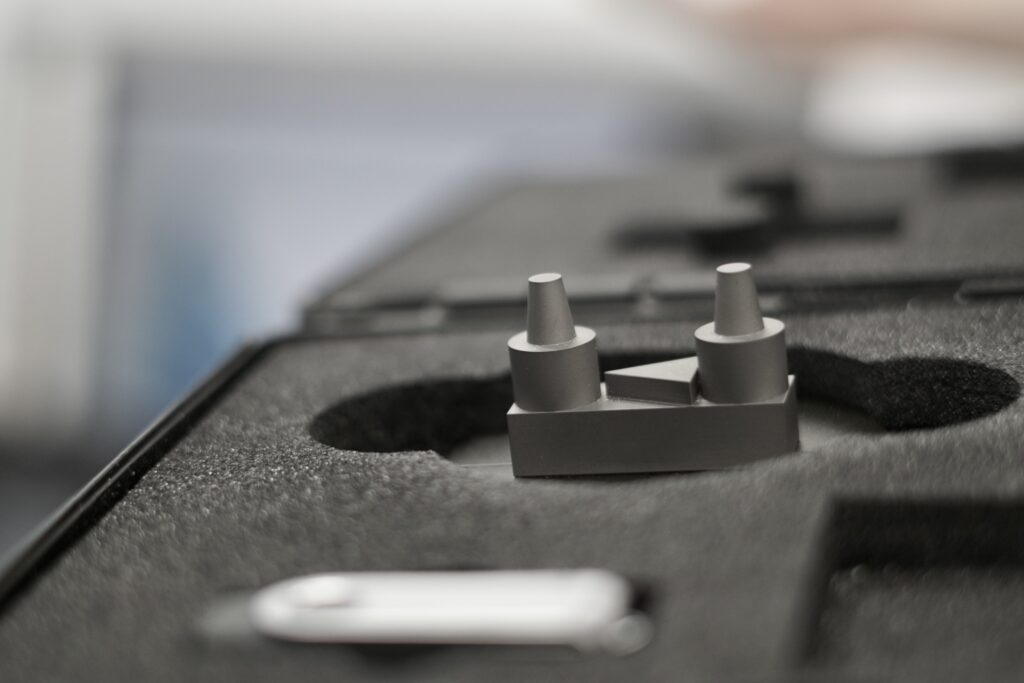
バリデーションチェック用の器具
耳型の代わりに特殊な形状の部品をセッティングしテストスキャンを実施します。
機械の中に事前に登録された設計図と
このスキャン結果を重ね合わせて差異が無いかを検証するそうです。
システム上、このバリデーションチェック作業を行わないとスキャンができないようにしているそうで、
不具合品が製造されてしまうことが無いように対策されているとのこと。
バリデーションが完了し、いよいよ3Dスキャン開始です。
青いレーザーを耳型に照射し、反射したレーザーをカメラで捉えることで座標データをスキャンします。
左右の耳型が30秒程度でスキャンできます。
モデリング
スキャンした3Dデータをもとに、シェルのモデリングの工程が行われます。
補聴器取扱店から届くオーダーメイド注文書には、「電話相談希望」というチェック欄があります。
もしチェックが入っている場合には、モデリングの前に補聴器取扱店まで電話をして、詳細な打ち合わせが行われます。
補聴器取扱店の担当者と、製造部門で実際にモデリングを行う担当者が直接打ち合わせを行うことはメーカーとしては大変さもある為、
間に営業社員が入って間接的な打ち合わせを行うメーカーも多いです。
これは双方、メリットもデメリットもある為、一概にどちらが良いとは決められませんが、
GNは直接打ち合わせを行なうことでより満足いただける製造を行おうとする姿勢のメーカーです。
一方的な指示であれば注文書への記載で事足りる場合もあるかと思いますが、
実際に装用される補聴器ユーザーからの訴えや販売員の知見とモデリング担当者の意見を交え、
モデリング担当者から提案を行うなどして双方向のディスカッションを行うことで
より満足度の高い補聴器を作るためのモデリングを行なっていきます。
シェル内に収めるレシーバーなどの部品の位置や角度も想定してモデリングされます。
なるべく小さい補聴器を希望されるお客様が多いので、いかにコンパクトに収められるかも腕の見せ所の一つです。
GNの充電式耳あな型補聴器の場合は、本体だけでなく
充電器も耳型に合わせて作られるオーダーメイドタイプですので、
充電器への納め方もモデリングされます。
3Dプリント
3Dプリンタは吊り下げ型のDLP方式。
先程モデリングされた3Dデータのシェル(機械が入る外側の部分)が3Dプリントされます。
シェルの材料はドロっとした特殊な液体。
この液体は紫外線(UV)を浴びると硬化します。
下からプロジェクターのようなもので、硬化させたい部分に紫外線を当てることで1層(0.05mm)分 硬化させます。
1層硬化させるごとに上部のプラットフォームが1層分ずつ持ち上がっていき、
それを繰り返すことで形状が出来上がっていきます。
複数のシェルがまとめてプリントされます。
よく見ると、
端の部分に補聴器ではない、四角い部分があります。
このテストケースと呼ばれる部分は、バリデーションを行うために印刷されていて、
製造の度に この部分の寸法を測定し、設計通りの寸法でプリントできているかの検証を行うそうです。
この検証に合格すると、今回プリントしたシェルすべてが品質上問題なしと判断されて製造工程に進むことができるそうです。
確かに、ほんの少しでもサイズに誤差があるとお客様の耳と合わず、意図しない隙間ができてしまったり、痛みの原因になってしまいますね。
刻印
さて、先程の3Dプリントで出来上がったシェル部分ですが、
このままではもう、誰の補聴器なのかわかりませんよね。
今からこのシェルに刻印が行われます。これが刻印を行う装置。
レーザーを当てることでシェルに掘り込みを行います。
機種名・製造番号・ユーザー名などがレーザーで刻印されます。
ただ、この時点では、単に字の形で掘り込みされているだけなのでほとんど読めません。
そこで、手作業で塗料を塗ります。
このように、塗料を塗り、拭き上げて乾くと…
彫り込みの形で綺麗に文字が残るという仕組みです。
※個人情報が含まれているため、画像をぼかして加工していますが、実際にはとてもくっきりしています。
ケーシング
これは、シェルの中に収めるレシーバーやアンプといった機械類。仕様によってサイズ・形状が様々。
先程のシェルの中にこういった機械を収めていきます。
この製造工程からは実際に機械に手を触れるため、静電気対策として技術者は静電作業靴を履かれています。
靴底から静電気を逃すことでスパークの発生を防止することができます。
技術者の腕からは何やらケーブルが…
腕に着けているケーブルはアースバンド。
静電気によって機械がダメージを受けることが無いように対策されています。
モデリングで決めたレイアウトに従って、シェルの中に機械を組み込んでいきます。
顕微鏡とピンセットを使って丁寧に機械を収めていきます。
接着・コーティング
シェルとフェイスプレートの接着も紫外線で硬化する接着剤が用いられます。
UV照射機も毎週バリデーションが行われているそうです。
前半で作成していたメス型を使って形のチェックが行われます。
切断・研磨
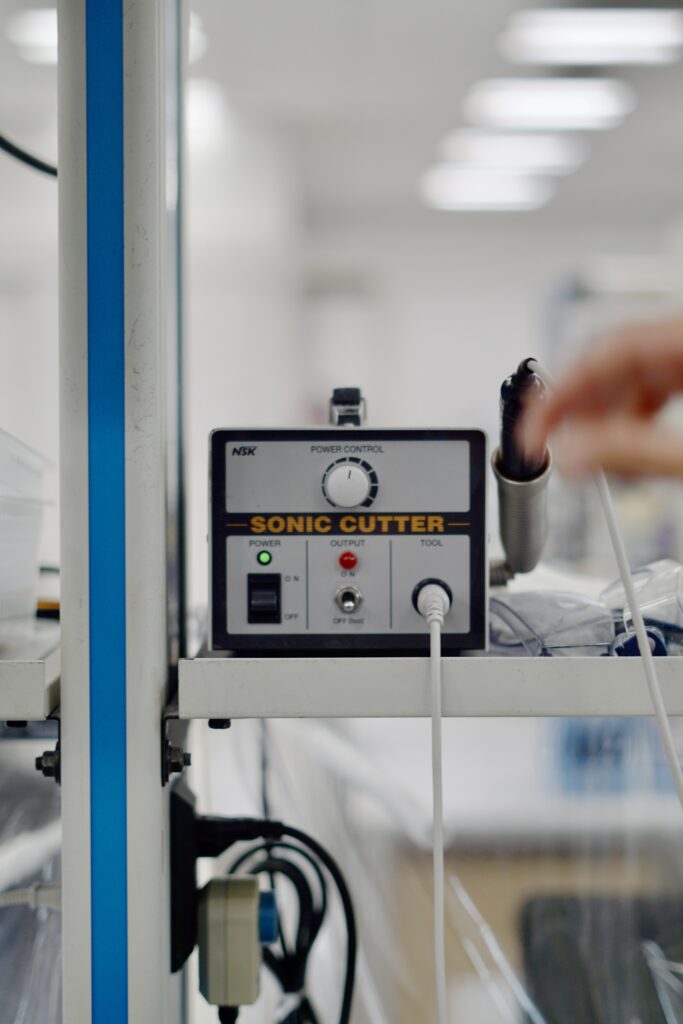
超音波カッター
毎秒数万回という超音波振動でカットする超音波カッターでフェイスプレートの切断が行われます。
超高速の振動で切り落とし。
切り落とした上で、事前に作成していたメス型にはめて、耳とどこが当たるかなどがチェックされ研磨作業が行われます。
「補聴器をつけると耳が痛い」といったトラブルが起きない為の対策です。
削った部分を研磨して
仕上がりとなります。
検査部門
出来上がった補聴器は、検査部門で厳しい検査を受けます。
数多くの特性機(補聴器の音の出方を正確に測定する機械)が並んでいました。
実際にその補聴器のスペックを満たしているかを機械が正確に判断します。
厳しい検査に合格した製品だけがお客様の元に運ばれます。
出荷の際には検査結果が添付されます。
出荷
基幹システムから出力されるピックチケットには商品名や付属品それぞれに対して、棚の番地が記載されているのでそれに従ってピッキングが行われます。
納品書や保証書をシステムから出力し
正確かつ丁寧に梱包されます。
これで完成となり、補聴器取扱店宛に迅速に出荷されます。
最後に
今回の工場見学の中で、何度も「バリデーション」や「対策」という言葉を伺いました。
工場内に飲食物の持ち込みが禁じられており、静電安全靴やアースバンドを使うなど、
様々な場面で不具合品を出荷しないための対策が講じられており、
取扱店とモデリング担当者の直接電話打ち合わせも行うなど、
品質に関してできることはやるという力強い姿勢を感じました。
私たち販売店はそれらの補聴器の音質調整を行い
お客様に納品させていただいております。
以前から、GNグループは、とてもユニークな補聴器メーカーだとは感じておりましたが、
今回の本社・工場見学にて、品質に関する真剣さを感じ、これからも安心してお客様にお届けできると感じました。
GNからは現在「ネクシア」という補聴器が発売されており、当店でも多くのお客様にお使いいただいております。
無料でお試しいただけますのでぜひご相談ください。
GNの補聴器はとても魅力的ですが、お客様はそれぞれ聴力や生活環境、音の感じ方が異なり、
より満足いただける補聴器メーカーが人それぞれ異なります。
当店ではGNをはじめ、全ての大手補聴器メーカーを取り扱っておりますので、
ぜひ様々なメーカーの補聴器の聴き比べを行った上で納得できる補聴器と出会っていただけたらと思います。
お客様からのご相談を心よりお待ち申し上げております。
.